Discover best practices in inventory planning to balance stock levels, reduce holding costs, and improve cash flow through effective demand forecasting.
Inventory Planning: How to Optimize Stock Levels and Reduce Costs
January 20, 2025
•
2 min read
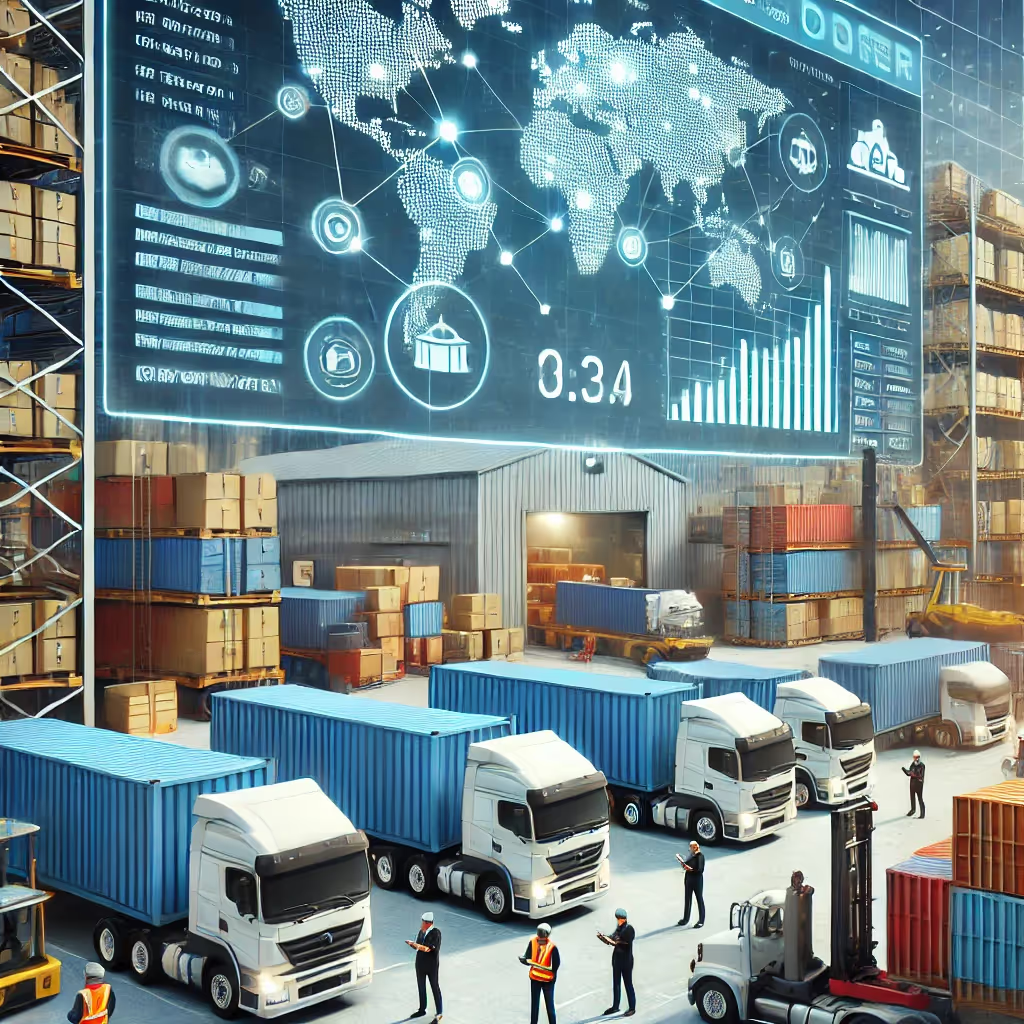
Introduction
Managing inventory effectively is crucial for businesses looking to reduce costs, meet customer demand, and prevent stockouts. But how do you strike the right balance between overstocking and running out of stock? This guide explores the best practices for inventory planning to improve supply chain efficiency.
What is Inventory Planning?
Inventory planning is the process of determining the right amount of stock to have on hand to meet demand while minimizing holding costs. It involves analyzing historical sales data, forecasting future demand, and optimizing reorder points.
Why is Inventory Planning Important?
- Prevents Stockouts – Ensures products are always available for customers.
- Reduces Holding Costs – Minimizes excess inventory that ties up capital.
- Improves Cash Flow – Optimizes procurement and reduces unnecessary spending
Best Practices for Effective Inventory Planning
- Use Demand Forecasting – Leverage historical sales data and market trends to predict future demand accurately.
- Implement Just-in-Time (JIT) Inventory – Reduce holding costs by ordering stock only when needed.
- Classify Inventory with ABC Analysis – Prioritize stock based on value and sales frequency.
- Monitor Supplier Lead Times – Work with reliable suppliers to ensure timely replenishment.
- Utilize Inventory Management Software – Automate stock tracking and improve real-time visibility.
How to Get Started with Inventory Optimization
- Assess your current inventory turnover rate.
- Set up safety stock levels to account for demand fluctuations.
- Regularly review sales data to adjust stock levels dynamically.
Looking to improve your inventory planning strategy? Contact us to learn how we can help!